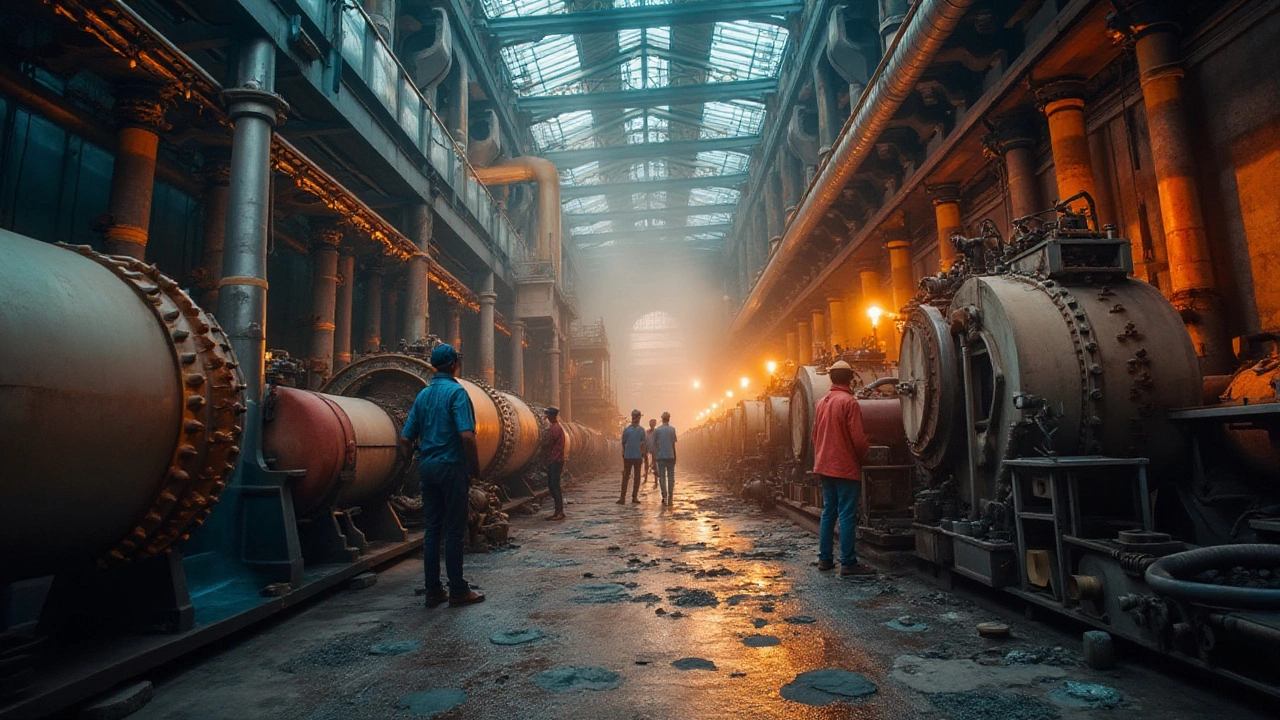
Sourcing Plastic: The Journey from Raw Materials to Manufacturing
Plastic is so entwined with our daily lives that it's easy to overlook where it comes from. Yet, the journey of plastic, from raw material to finished product, is an intricate process involving multiple steps.
The origins of plastic materials begin with basic raw resources, primarily natural gas and crude oil. These resources are transformed into chemical building blocks through various procedures. The conversion of these blocks into polymers lays the foundation for all plastic products we use.
Manufacturers work with a network of suppliers across the globe to obtain plastic pellets, which are distributed throughout different markets. This global supply chain ensures that industries have the materials they need to produce everything from simple water bottles to complex automotive components. Alongside logistical considerations, quality and sustainability are pivotal aspects that manufacturers continue to prioritize in this process.
- Understanding Raw Materials
- The Transformation Process
- Global Suppliers and Markets
- Ensuring Quality and Sustainability
Understanding Raw Materials
If you've ever wondered what lies at the heart of the various plastic products that surround us, it all starts with raw materials steeped in the history of human innovation. Plastics largely begin their life from the extraction of fossil fuels, including natural gas and crude oil. These resources may be buried deep within the Earth's crust, and they undergo a series of sophisticated and meticulous processes to turn them into the polymers that eventually become plastic. The sheer volume of transformation these materials undergo is quite literally a journey from dark depth to vibrant utility. But what are these initial forms like, and why are they so crucial?
Natural gas, a pivotal ingredient in plastic manufacturing, is primarily composed of methane and other hydrocarbons. It's a flexible raw resource not only for its applications in energy but also for its role in plastic production. The gases are processed through cracking – a term that aptly describes the breaking apart of larger molecules into more manageable building blocks. This technology is continually innovating, seeking to optimize both yield and environmental impacts. The byproducts and fragments that emerge are foundational in forming the ethylene and propylene, core substances that later polymerize to create various kinds of plastic suitable for multiple uses from food packaging to electronics.
Meanwhile, crude oil, the dark, viscous liquid often associated with energy production and transportation, plays its part. Through an intricate method known as fractional distillation, crude oil is separated into component parts based on different boiling points. Out of this separation emerge the naphthas, alkanes, and other fractions that are crucial in the petrochemical industry, setting the stage for them to become indispensable in the manufacture of polymers. This entire process is not just about mechanical separation, but about molecular transformation, a symphony of chemistry at work.
The importance of sourcing from fossil fuels doesn't go unacknowledged in the industry. There is increasing pressure to balance the reliance on such finite resources with sustainability and environmental stewardship. Innovations in bio-based plastics, derived from renewable resources like corn or sugarcane, showcase a growing trend towards greener alternatives. According to a report by IHS Markit, "the production of bio-based plastics is expected to grow by 21% annually, a testament to the sector's drive towards environmental responsibility."
"The balance between the utilization of traditional raw materials and innovative bioplastics is essential," says Dr. Maya Liang, a leading chemist in the field of sustainable materials. "We're on a path that needs both, understanding ecological impacts and paving the way for the next generation of manufacturing."
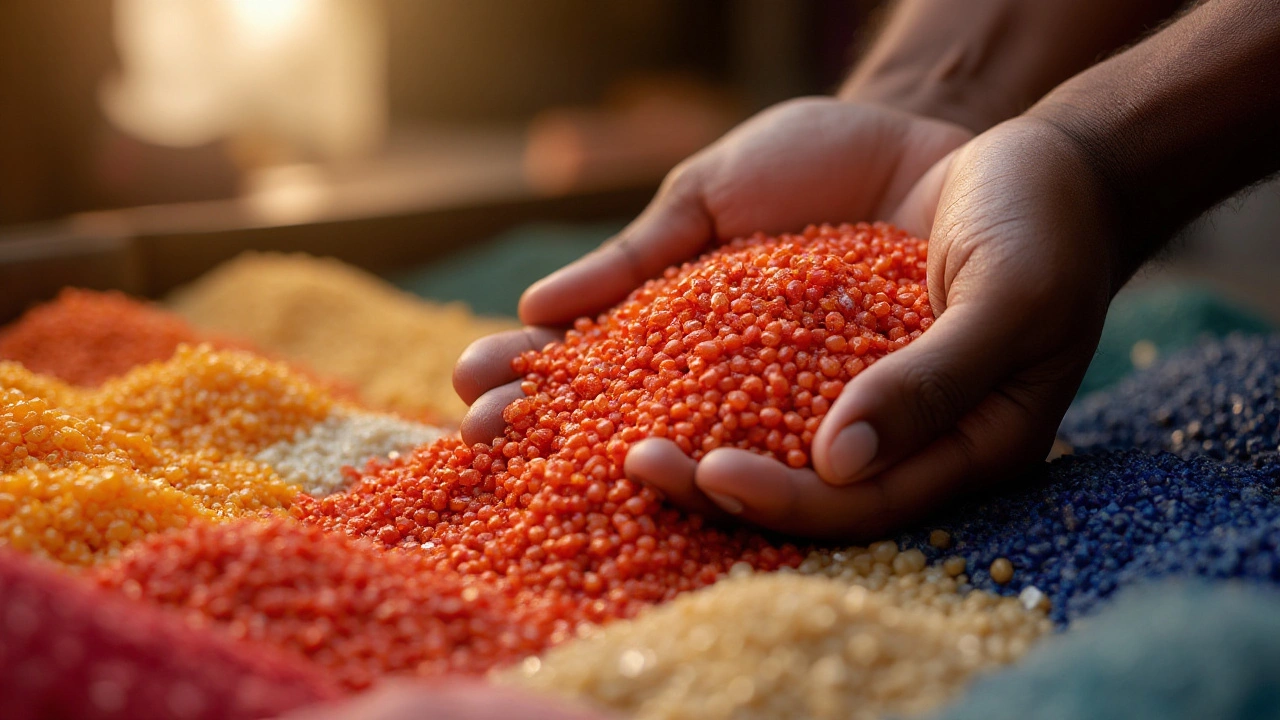
The Transformation Process
At the heart of plastic sourcing lies the fascinating transformation process that converts simple raw materials into the versatile plastics we encounter daily. This journey starts with crude oil and natural gas, the building blocks of countless products. These resources undergo a process called cracking, where they are subjected to high heat to break down large molecules into smaller ones. Ethylene and propylene, key chemicals in the creation of plastics, emerge from this stage, setting the groundwork for subsequent transformations.
The next significant step is polymerization. During this phase, small molecules known as monomers are chemically bonded to form long chains called polymers. This transformation is crucial as it determines the specific type of plastic being produced. For instance, polyethylene, the world’s most common plastic, results from the polymerization of ethylene. These polymers are typically transformed into plastic pellets, a critical intermediate that manufacturers receive. The conversion processes are highly technical, involving catalysts that accelerate the bonding process without compromising quality or consistency.
A noteworthy aspect of the transformation is the extrusion and pelletizing stage. This is where the polymers are heated, melted, and forced through a die to form strands, which are then cooled and chopped into small, uniform pellets. Achieving consistent size and quality is paramount, as it affects the plastic's properties during the molding and manufacturing stages. The meticulous process ensures that these pellets meet the stringent standards required by industries ranging from packaging to automotive design.
Innovations and Technological Advances
The transformation process has seen massive innovation driven by the necessity for efficiency and environmental consciousness. Technological advancements like advanced metering and precise control systems have allowed manufacturers to refine the polymerization process, minimizing waste and maximizing material usage. Another emerging technology is bioplastics, which utilizes renewable resources like corn starch, drastically reducing dependence on fossil fuels. As noted by a report from Plastics Europe, "Innovations in the production process continue to push boundaries, leading to lower energy consumption and reduced emissions."
In exploring global suppliers and markets, it becomes evident that manufacturers seek not only raw materials but also cutting-edge technology to maintain a competitive edge. The diversity of options in polymers, from high-density polyethylene to polyvinyl chloride, offers flexibility in applications while demanding precision in production. The synergy between technological improvement and environmental responsibility underpins the modern-day transformation process, fueling an industry pivotal to countless sectors globally.

Global Suppliers and Markets
When it comes to sourcing plastic, the global market plays a pivotal role. Over the past few decades, the industry has witnessed significant shifts in how raw materials are supplied and distributed worldwide. Some of the main players in the market include countries rich in fossil fuels, like the United States, Saudi Arabia, and Qatar. The conversion of these resources into usable plastic involves extensive industrial operations. Remarkably, the United States is known as one of the leading producers of polyethylene, a polymer used widely across various industries. This dominance in the market can be largely attributed to the nation's abundant supply of shale gas, which provides a cost-effective source of ethylene, a key building block for polyethylene.
In the global context, China is another major hub, not just because it imports a large portion of the world's raw plastic material but also due to its significant contribution to plastic manufacturing. With a vast network of facilities powered by cutting-edge technology, China has cemented its status as a powerhouse in plastic production. Their ability to efficiently process polymers into finished goods has made China a central figure in the international supply chain. Additionally, the influence of European companies, such as BASF in Germany and INEOS in the UK, demonstrates the importance of regional producers who balance production efficiency with sustainability initiatives.
"The global plastic market is expected to reach USD 750.1 billion by 2028, with Asia Pacific holding the largest share," according to a recent market analysis by Grand View Research.
The dynamics between these suppliers and the market demands are endlessly fascinating, as factors such as geopolitical stability, trade policies, and environmental regulations weave complex patterns of dependence and competition. Oil-rich regions like the Middle East have invested significantly in creating petrochemical complexes that can deliver a steady stream of raw materials for plastic production. Saudi Arabia and Qatar, among others, have prioritised diversifying economic dependencies on oil by boosting their capacities in polymer production facilities, thus altering the global supply landscape.
Geographically strategic locations, like Singapore, serve as critical logistics hubs, allowing for efficient transportation and storage of plastic resins. The interplay of sea lanes and air routes ensures that even regions with limited internal production capabilities can maintain a steady supply of materials. Organizations have to dance around these logistical nuances to keep pace with the competitive market. One important aspect they focus on is the reduction of carbon footprint during the transport stage. Another emerging trend is the preference for suppliers who comply with international environmental and ethical standards. These zero-tolerance policies towards pollution and unhealthy labor practices are transforming the supplier-consumer relationships.
The plastic supply chain is truly a global endeavor, woven together by a multitude of factors ranging from technological advancements to economic policies. As manufacturers continue to adapt to the ever-evolving market conditions, their success hinges on strategic partnerships with suppliers who can deliver both quality and sustainability in the form of plastic polymers and materials. To navigate the complexities of this market, manufacturers often employ teams of experts dedicated to ensuring optimal sourcing strategies that keep costs down while meeting consumer demands for more environmentally friendly products.
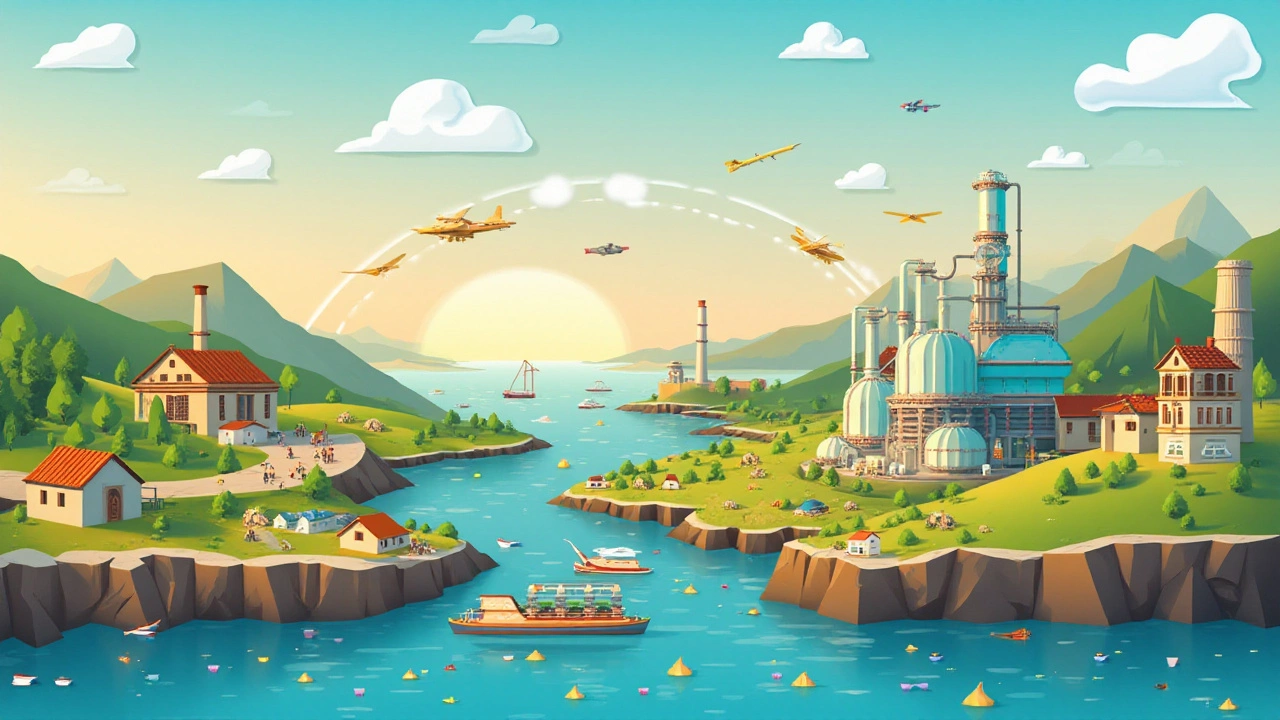
Ensuring Quality and Sustainability
Manufacturers in the plastic industry face the dual challenge of maintaining high standards of quality while also addressing growing concerns about environmental impact. At the core of plastic sourcing, ensuring that products adhere to rigorous quality benchmarks is a top priority. Compliance with international standards such as ISO 9001 ensures that every batch of plastic meets specific criteria for durability and reliability. Companies regularly conduct quality checks and audits along the supply chain to ascertain that the materials sourced are devoid of deficiencies that could compromise the integrity of the final products. These steps are integral to instilling trust not only among manufacturers but also with the end-users who rely on these products every day.
Sustainability, on the other hand, has become a driving force behind innovation in the industry. The focus now is on reducing the carbon footprint associated with manufacturing processes. Many companies are investing heavily in research and development to create alternative bio-based plastics which are biodegradable. They seek to balance effectiveness and environmental impact. An interesting trend is the growing use of recycled plastics, where advancements allow for the production of high-quality plastics that incorporate significant percentages of recycled content without sacrificing performance. Using recycled materials is not only beneficial to the environment but also economically advantageous in mitigating raw material costs.
Industry Initiatives and Policies
Industries are also working collaboratively with governments to enhance the sustainability measures within the plastics sector. Many regions have laid down stringent policies that aim at reducing plastic waste, thereby pushing companies to innovate continuously. For instance, the European Union has created directives that require manufacturers to incorporate a minimum percentage of recycled content in their products. This serves as a catalyst for an industry-wide shift toward a circular economy model where waste is minimized, resources are used wisely, and recycling is prioritized.
One critical aspect of ensuring sustainability is the commitment to transparency, allowing consumers to understand the efforts taking place 'behind the scenes' of their products. Brands are now showcasing certifications and labels that highlight their compliance with environmental standards, thus empowering informed consumer choices. An emphasis is placed on 'green' marketing initiatives to align with customer values and expectations.
Citing a recent report by the Ellen MacArthur Foundation, "The commitment to develop a circular plastics economy is no longer optional but a business imperative to ensure both economic resilience and environmental protection."
The journey toward quality and sustainability is ongoing, with many multifaceted strategies in place. Manufacturers know long-term viability depends on their ability to balance business operations with responsible stewardship of resources. By creating symbiotic relationships with suppliers who share this vision, the industry is collectively moving towards a future where both high-quality and eco-friendly practices thrive in tandem.
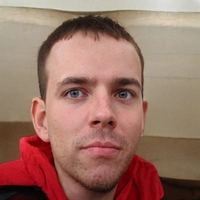
Jedrik Hastings
I am an expert in the manufacturing industry, focusing primarily on the evolving landscape of manufacturing in India. My work allows me to analyze various advancements and challenges in the sector. I enjoy writing about these developments and offering insights into how they impact businesses globally. In my free time, I like to delve into historical manufacturing practices and design future strategies. My passion for the field is driven by a desire to contribute to sustainable and innovative manufacturing solutions.
Categories
- Manufacturing and Industry (11) Food Processing (11) Small Scale Manufacturing (10) Pharmaceutical Manufacturing (9) Automobile Manufacturing (7) Electronics Manufacturing (7) Manufacturing Business Ideas (7) Steel Manufacturing (7) Manufacturing Schemes and Government Support (6) Plastic Manufacturing (4)
Recent Post
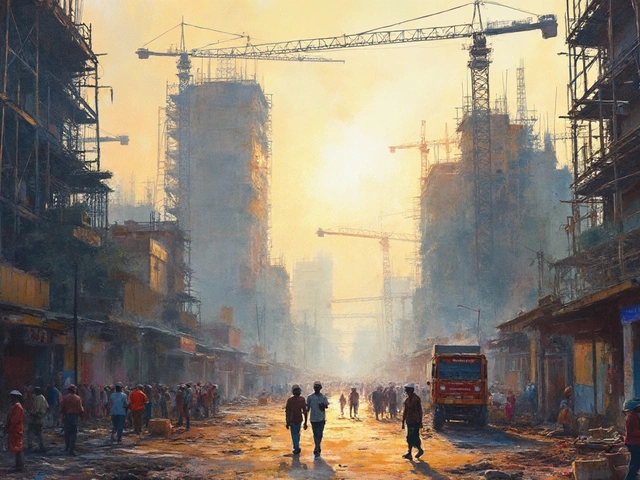
Write a comment