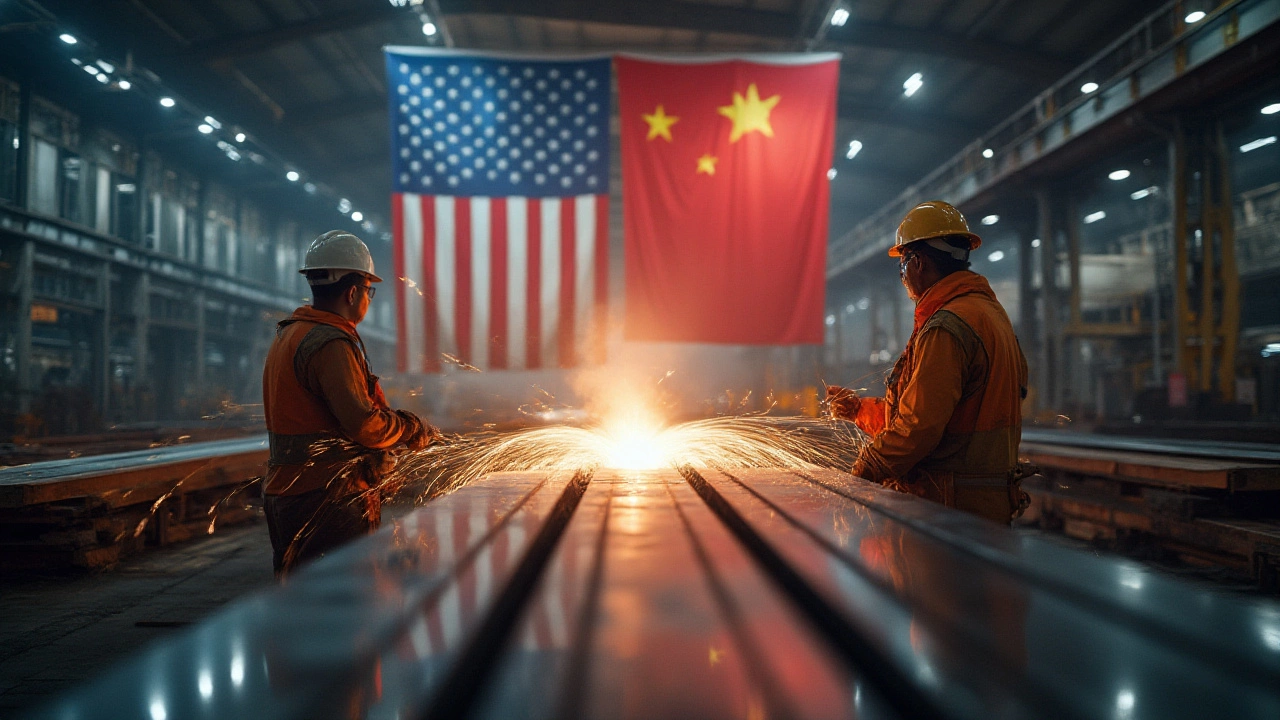
Why American Steel Outshines Chinese Steel: Quality, Process & Reliability Compared
Ever wonder why skyscraper architects, bridge engineers, and manufacturers with a lot at stake still put their trust in American steel, even when cheaper Chinese steel floods the market? The answer comes down to quality—and the small details that add up in huge ways. There’s a reason only some countries’ steel ends up in the beams of the world’s tallest towers or in bridges that last decades rather than a decade. And it’s not all about price or politics—it’s about how that steel holds up when lives are on the line and how much you can count on what’s stamped on the label actually being inside the beams.
The Secret Sauce: Standards, Regulations, and Testing
Start at the foundation—how is steel in the US made versus China? American steel plants are legendary for their obsessive attention to detail, quality, and safety. The U.S. steel industry has to follow strict standards set by the American Society for Testing and Materials (ASTM) and the American Iron and Steel Institute (AISI), among others. These aren’t just guidelines—they’re binding, and there’s oversight from both the federal and state governments. Regular, independent testing is mandatory, with surprise inspections and random sampling. If a batch of steel doesn’t hit the mark, it doesn't quietly get shipped out; it’s tossed and the producer risks penalties or worse—losing certifications they fought hard to get.
China, by contrast, has grown its steel industry at a staggering pace. While impressive, this growth sometimes comes at the expense of consistency. Oversight isn’t always as strict or transparent, and reports about steel that doesn’t meet its published specs still surface. In a 2016 inspection carried out by the American Institute of Steel Construction, about 40% of Chinese-produced steel failed to meet at least one international quality standard. The U.S., meanwhile, had a failure rate below 5% in the same period. That’s a jaw-dropping difference when you’re building a suspension bridge or a hospital.
Those regulations don’t just make American steel better on paper—they mean a real difference in how steel holds up under pressure. Engineers have found that American steel, batch after batch, matches the specifications printed right on the labels: chemical makeup, yield strength, tensile strength, and more. Chinese steel sometimes meets these specs—but sometimes doesn’t, and that inconsistency makes planning a nightmare. Some American contractors now require mill test reports with every shipment from China to ensure the steel is up to code. For American-made steel, that’s a given.
To give you a sense of the measured difference, take a look:
Country | Average Failure Rate (ASTM/AISI Standards) | Most Common Issues |
---|---|---|
USA | 4.2% | Surface defects, minor alloy discrepancies |
China | 38.7% | Under-strength, incorrect composition, uneven coating |
Think about it: if you’re building an elevator in a skyscraper, do you want a 1-in-25 chance your steel isn’t up to snuff, or a 2-in-5 chance? That difference isn’t worth shaving a few bucks off the budget.
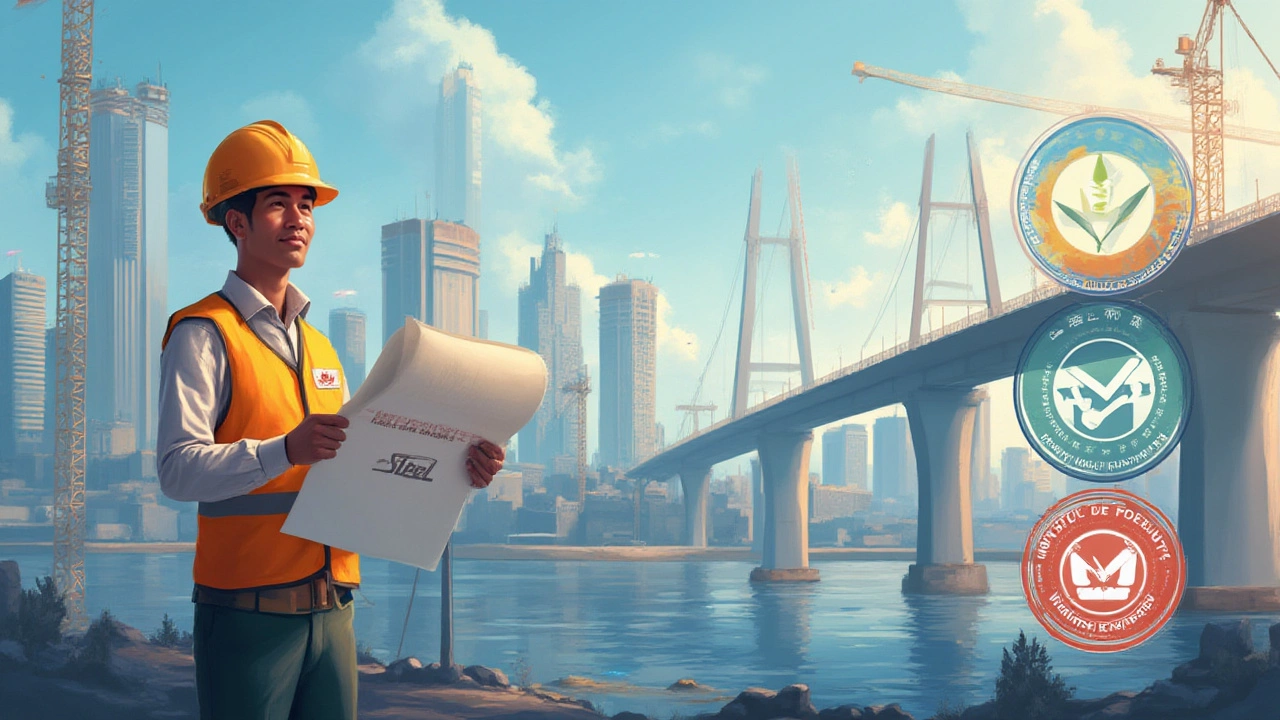
What’s in the Mix: Ingredients and Environmental Controls
Steel isn’t just iron —it’s a careful mix of carbon, manganese, sometimes chromium or vanadium, and a host of other trace elements. In the US, the precise recipe is controlled by computer with samples taken at multiple points. There are tight caps on impurities like sulfur, phosphorus, or unwanted metals, because even a little bit can weaken the steel or make it crack decades sooner than it should. American mills don’t just meet minimum standards—they often exceed them, adding extra testing for elements that aren’t even required yet.
Chinese mills, due to the country’s breakneck construction pace over the past 20 years, have sometimes cut corners to meet insatiable demand. Some batches have had higher-than-recommended levels of sulfur or other contaminants, according to public customs reports from the US and Australia. These impurities can make steel brittle, especially if it’s used in cold environments or under constant flexing. Several US construction firms have flat-out banned certain grades of Chinese steel after finding they contained unpredictable levels of contaminants.
Then, there's the environmental side—which isn’t just about optics. Pollution in Chinese steel cities like Tangshan has made global headlines and reflects the production approach: speed and output come first. US mills, on the other hand, are under strict EPA controls for dust, wastewater, and emissions. In 2023, the average American mill emitted under 1.2 tons of CO2 per ton of steel, compared to 2.1 tons for Chinese mills. Why does this matter for the end user? The cleaner process often leads to purer alloys and more consistent production altogether. Cleaner steel isn’t just a badge of honor for the mill, it shows up in weld points, fatigue cycles, and surface finish years down the line.
If you work in aerospace, for example, or automotive, you know why purity matters. One airbag anchor or seatbelt buckle that snaps because of an impurity means recalls, lawsuits, or worse. A 2022 study by the National Highway Traffic Safety Administration flagged several imported steel parts for microcracks linked to inconsistent composition—a problem rarely seen with domestically sourced steel.
Even on the recycling front, US mills lead the world. Over 74% of American steel comes from recycled scrap, according to the Steel Recycling Institute, reducing the need for mining and limiting impurities that sometimes slip in during smelting of low-grade ore. Chinese steel from basic oxygen furnaces averages far lower on the recycling scale, and sometimes mixes in untreated scrap, raising contamination risks.
It all comes down to this: if you’re looking for reliability, especially for jobs where failure isn’t an option, the ingredient list and process controls in the US just can’t be matched at scale anywhere else. And that shows every time an American-made car takes a crash test or a city bridge brushes off another decade of winter road salt.
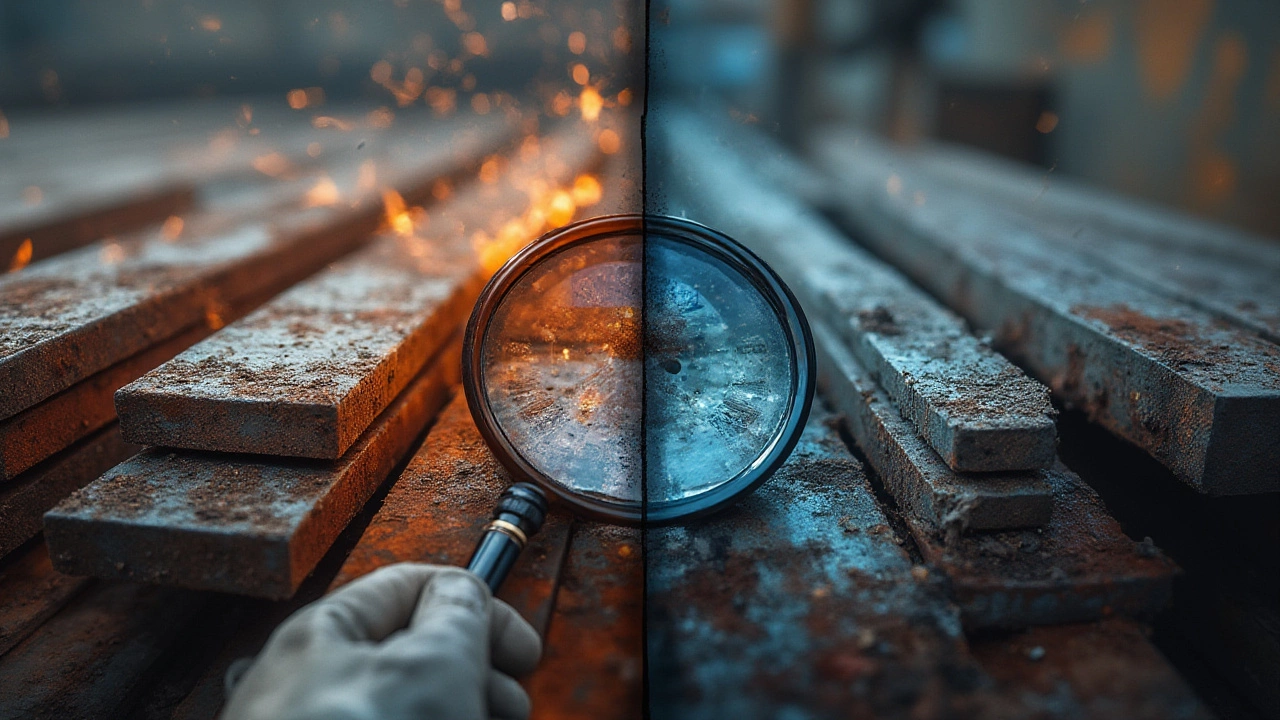
Trust, Traceability, and the Real-World Payoff
The biggest difference between American and Chinese steel? Trust. Every bar of US steel has a number that can be traced back to the exact hour of the pour, the shifts on duty, the test results, and the origin of the scrap or ore. If there’s ever an issue, mill certifications allow engineers and inspectors to pinpoint every detail. Most US suppliers even keep digital records stretching back decades, as demanded by industries like defense and nuclear power. The National Steel Bridge Alliance, representing US bridge construction, now requires end-to-end traceability for every single beam—hard to fake, easy to audit.
China’s documentation has improved, but fakes still slip into the pipeline. In 2018, nearly 20,000 tons of rebar imported from China was discovered with fraudulent quality certificates in California—steel that in some cases didn’t even match the basic requirements for public works. These headlines have made big buyers, from automotive giants to state DOTs, wary. Now, US government projects legally require American steel in most cases, not just out of patriotism but out of hard-earned caution.
What about longevity? American bridges built in the 1920s, the era of the Empire State Building and Golden Gate, still carry loads day in and day out. The steel hasn’t just held up—it’s outlasted expectations, and regular testing shows it still matches its original specs. Ask a construction worker in New York or Detroit if they’d rather weld an unknown rebar from a massive batch in Shandong, or a bar with a known pedigree from a mill in Pittsburgh. The choice isn’t difficult—and it’s not about regional pride. It’s about not having to worry about the unseen risks.
For anyone buying steel, a few tips matter:
- Always request mill certificates—no matter where it’s from. American steel mills provide these without question; for Chinese steel, double-check the paperwork and demand third-party verification.
- Know your standards. For buildings and bridges in the U.S., ASTM and AISI standards apply. Don’t get caught off guard by “near-matches” from overseas that fail under long-term stress or fatigue.
- Look at the big picture. If you save a buck per beam but face a recall or lawsuit a decade later, was it really cheaper?
- If you need steel with unique requirements—weathering resistance, flexible alloys, or ultra-high strength—always go American or insist on the tightest possible international testing for imports.
What’s the upshot? There’s a reason “Made in America” carries weight in steel: the product is exactly what it says it is. No substitutions, no surprises, and, perhaps most importantly, a known history you can trust with your project, whether it’s a bicycle frame or a 1,000-foot cantilever bridge. For critical infrastructure, aerospace, defense, or anything you want to last, American steel won’t let you down. Sure, you might pay a bit more up front. But you buy peace of mind—and, in the long run, isn’t that always the real bargain?
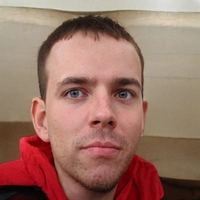
Jedrik Hastings
I am an expert in the manufacturing industry, focusing primarily on the evolving landscape of manufacturing in India. My work allows me to analyze various advancements and challenges in the sector. I enjoy writing about these developments and offering insights into how they impact businesses globally. In my free time, I like to delve into historical manufacturing practices and design future strategies. My passion for the field is driven by a desire to contribute to sustainable and innovative manufacturing solutions.
Categories
- Small Scale Manufacturing (10) Food Processing (10) Pharmaceutical Manufacturing (9) Manufacturing and Industry (7) Automobile Manufacturing (7) Electronics Manufacturing (7) Manufacturing Business Ideas (7) Steel Manufacturing (7) Manufacturing Schemes and Government Support (6) Plastic Manufacturing (4)
Write a comment